A baffle is an integral part of the vessel's mixing system that promotes better flow of fluids for maximum efficiency. Its primary function is to prevent the swirling in agitation by converting the swirling into a desired flow pattern.
Traditional Baffle Designs in Glass-Lined Vessels
The various types of traditional baffles used in glass-lined vessels are depicted in the diagram below (Figure 1). Depending on your process objectives and the characteristics of your product, one baffle type may be more suitable than another for your application.
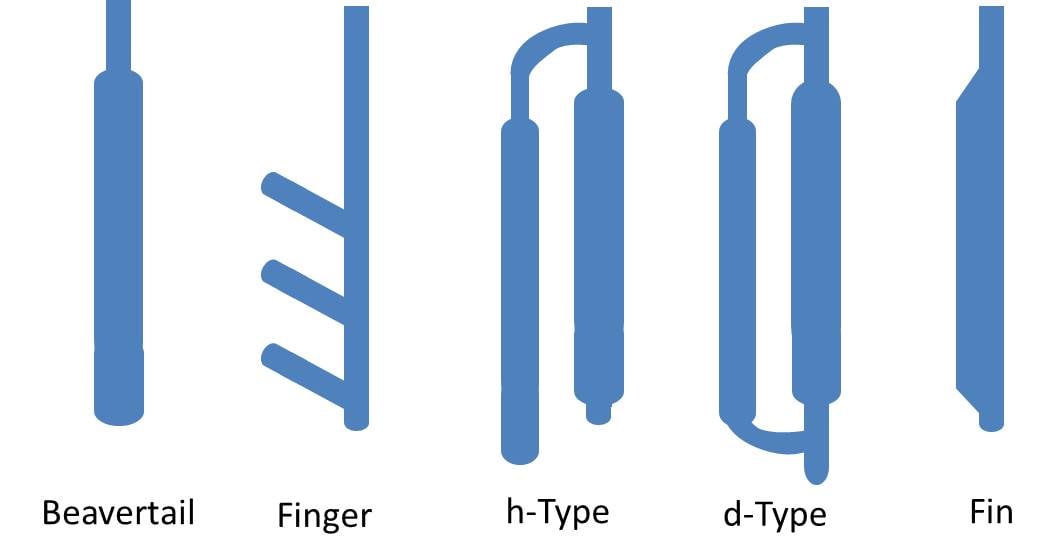
Figure 1. Traditional Baffle Configurations
The most commonly used design that offers effective performance for the majority of processes is the beavertail baffle (which, consequently, is the DDPS standard flange-mounted design). It can be conveniently installed through one of the standard nozzles on a reactor head, enabling easy, no-entry installation and removal (unlike the other types shown above which are holder-mounted and require vessel entry to install). Additionally, the beavertail baffle encases a temperature sensing system and has proven to offer high performance even at low liquid levels.
Beavertail baffles and other traditional units are specifically designed to hang from flanges in the vessel’s top head to ensure the integrity of the vessel lining. While this offers effective mixing, there are limitations and inefficiencies created by this arrangement. Traditional glass-lined reactors have employed a single baffle over multiple baffles mainly due to the challenge of attaching baffles to the reactor wall and encapsulating them with glass. Additionally, since mounting flanges are needed for process monitoring, insertion of cleaning devices, and the introduction of reactants, no more than two baffles are typically used due to the limited space in the head.
OptiMix Baffles
The OptiMix design solves the issues faced by traditional baffle installations by welding the reactor wall prior to coating all steel surfaces with glass. (Before this design, wall-mounted baffles were only available on metallic reactors). This new configuration employs three glass-lined baffles, rather than the single baffle used in conventional glass-lined equipment. As a result, mixing times are reduced by approximately one-third through improvements in heat and mass transfer, solids suspension and distribution, gas dispersion and gas flow rates.