Determining the desired flow pattern of the material in your reactor is dependent on your agitation objectives. There are two types of flow patterns that can be created – axial flow and radial flow. They are clearly illustrated in the figures below:
Figure 1. Axial Flow
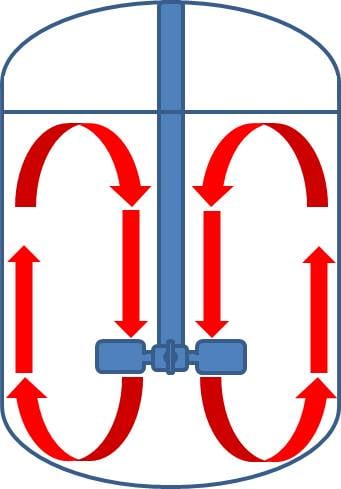
Figure 2. Radial Flow
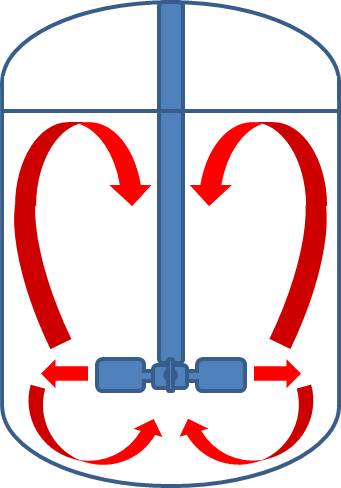
In axial flow, the most common mode of operation, the agitator pumps down the axis of the vessel and up the wall (see figure 1). This flow is designed to produce high flow to power ratio. Agitators that produce this movement are typically run at a relatively high rotational speed and are suitable for applications that require high product flow and low turbulent energy. Suspending settling solid particles and low viscosity bulk blending are examples of processes that work well utilizing axial flow.
Radial flow propels liquid outward from the agitator blade and revolves around the vessel axis, producing upper and lower circulation loops (see figure 2). While axial flow can be carried out with or without the use of a baffle, radial flow should always be operated with baffles to enable circulation between the top and bottom circular flows that are created from this flow pattern. Radial flow is ideal for de-agglomerating solids, dispersion and emulsion.