Despite the numerous advantages of glass-lined equipment, one drawback is the relatively low thermal conductivity. To offset this shortcoming, jackets are used to assist in heating and cooling vessels. Heat transfer fluids are passed through these jackets to add or remove heat to and from the process.
The two main jacket options are:
Conventional Jackets
The single jacket, also known as a conventional jacket design, consists of an outer jacket which surrounds the vessel. Heat transfer fluid flows around the jacket and is injected at high velocity via nozzles. The temperature in the jacket is regulated to control heating or cooling.
The single jacket is the “traditional” or “standard” design for glass-lined reactors and has been around the longest. Tried and true, this solution does provide the best pricing for a cost-conscious purchaser but there are a number of limitations that need to be taken into account:
- Adjustment of fluid temperature in the cooling jacket can take many minutes on larger sized vessels.
- Variance in temperature can occur between the side walls and bottom of vessel.
- Formation of hot/cold spots at the jacket inlet points is prevalent due to the temperature control valve.
Half-Pipe Coil Jackets
The half-pipe or split-coil jacket (referred to by DDPS as HemiCoil®) consists of a welded half pipe that wraps around the outside of the vessel, creating a circular path for the heat transfer fluid to pass through. In a split-coil jacket, heating and cooling media flow through the pipe coils with high velocity and turbulence. As a result, film coefficients and heat transfer rates are higher than in conventional jackets. Vessel contents heat up and cool down, and the heat transfer circuit drains much faster-saving energy and reducing batch time.
With the split-coil design, only the diameter of the pipe - not the unsupported height of the inner vessel - must contain the jacket pressure. This permits the safe use of much higher pressures within the coils than is possible in conventional jacketing: 450 psig at 500°F is the standard operating limit.
The split-coil reactor design is ideally suited to multiple zone arrangements as well as superimposed parallel circuits. Separate zones (Figure 1) offer the best versatility and efficiency, reducing pressure drop while keeping overall heat transfer rates high. This arrangement is particularly applicable to heating steam/cooling water media. Additionally, the shorter runs of coil piping decrease the pumping energy required for fluid circulation.
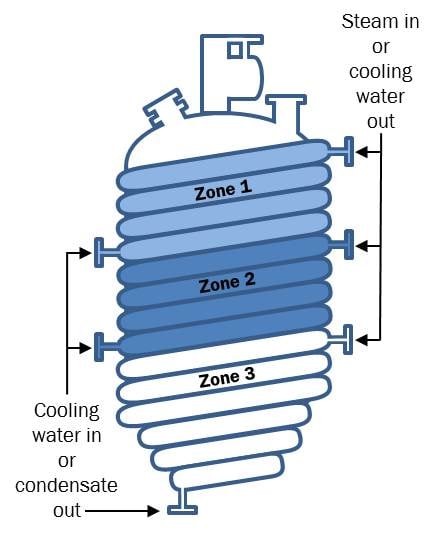
Figure 1
Parallel circuits (Figure 2) promote most effective use of the heat transfer properties of incompatible media such as heating steam/cooling brine or heating oil/cooling water. The arrangements shown here are typical; depending on vessel size and process requirements, each circuit may be divided into two or more zones.
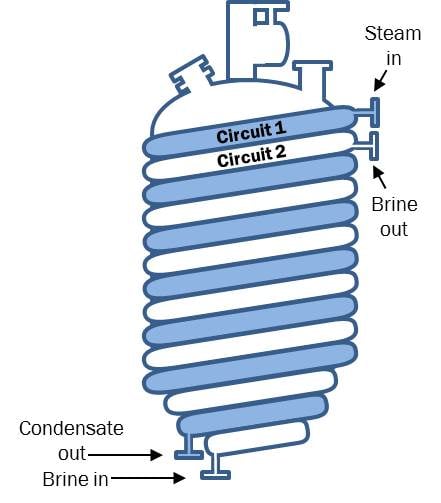
Figure 2