There are various heat exchanger solutions, and the different styles work better for some applications than others.
While there are many variations, the three main types are categorized as follows:
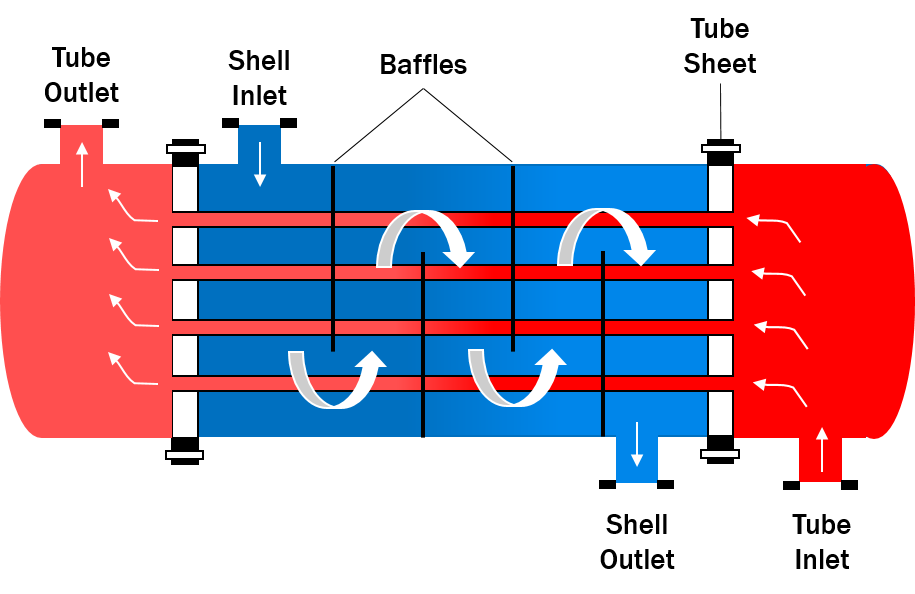
Shell-and-tube heat exchangers – these continue to remain a steadfast pillar in the chemical process industry due to their versatility. The design consists of a bundle of tubes containing fluid that run longitudinally through a shell holding a second type of fluid. Fundamentally, the shell fluid flows over the tubes, enabling heat transfer to take place.

Plate-based heat exchangers – these designs feature plates that enable the fluids to be exposed to a larger surface area than other designs. The two most popular types of plate HE’s are the welded-plate and gasketed-plate styles. Their compact designs make them advantageous for use in small spaces and the materials of construction (usually stainless steel or alloy construction) enable them to be used in operations that require high pressure and temperature allowances.
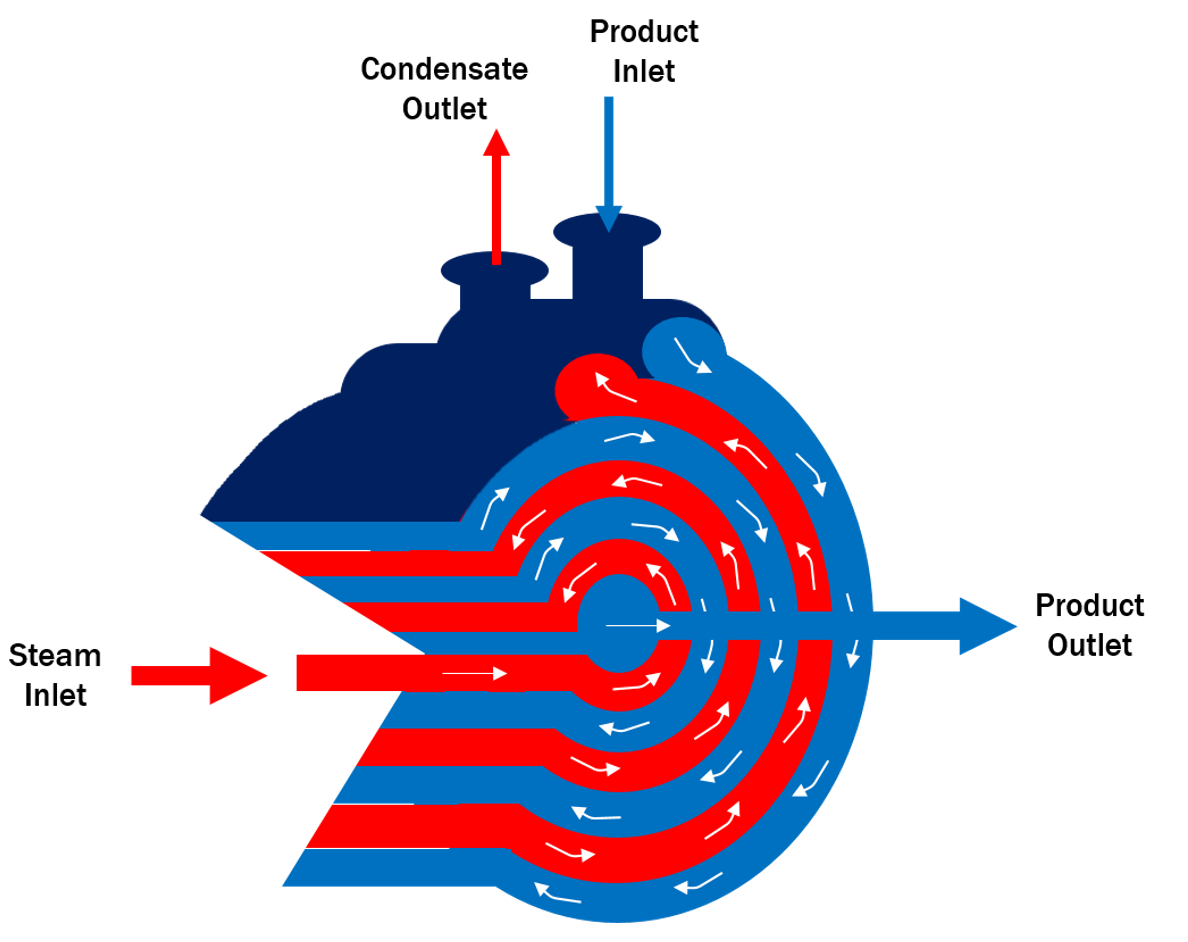
Coil/Spiral heat exchangers – In this arrangement, two fluids counter-flow parallel to one another through a set of helical tubes. With a compact design, these units provide excellent thermal efficiency in demanding applications and have a lower fouling tendency, making them a viable choice for difficult services.
Again, there are many more types of heat exchangers than just the three listed above, but this gives you a sense of the three most popular designs.