Exploring System Configurations with De Dietrich's Powder Pump System: A High-Level Overview
Pneumatic conveying is an essential process in many industries, allowing for the efficient and safe transportation of solids through pipelines using air or other (usually inert) gas. Depending on the specific needs of your operation, there are various system arrangements available to optimize the conveying process. In this post, we’ll provide a high-level overview of several key system arrangements for pneumatically conveying solids using De Dietrich’s Powder Pump System.
1. Vacuum Conveying System with the Powder Pump System
Overview:
A vacuum conveying system uses a vacuum to transport materials through a pipeline. This method is particularly useful for handling fine powders, granules, and other dry bulk materials. The system creates a vacuum at the receiving end, drawing materials through the pipeline from the supply point.
Applications:
- Ideal for transferring sensitive or hazardous materials.
- Commonly used in industries such as pharmaceuticals, food processing, and chemicals.
Benefits:
- Reduced risk of contamination and dust emissions.
- Gentle handling of materials, minimizing product degradation.
For more information about the specific functionality of our Powder Pump system, check out this download: Basic Function Overview
2. Mobile Conveying Option (Cantilevered or Installed Directly on Vessel)
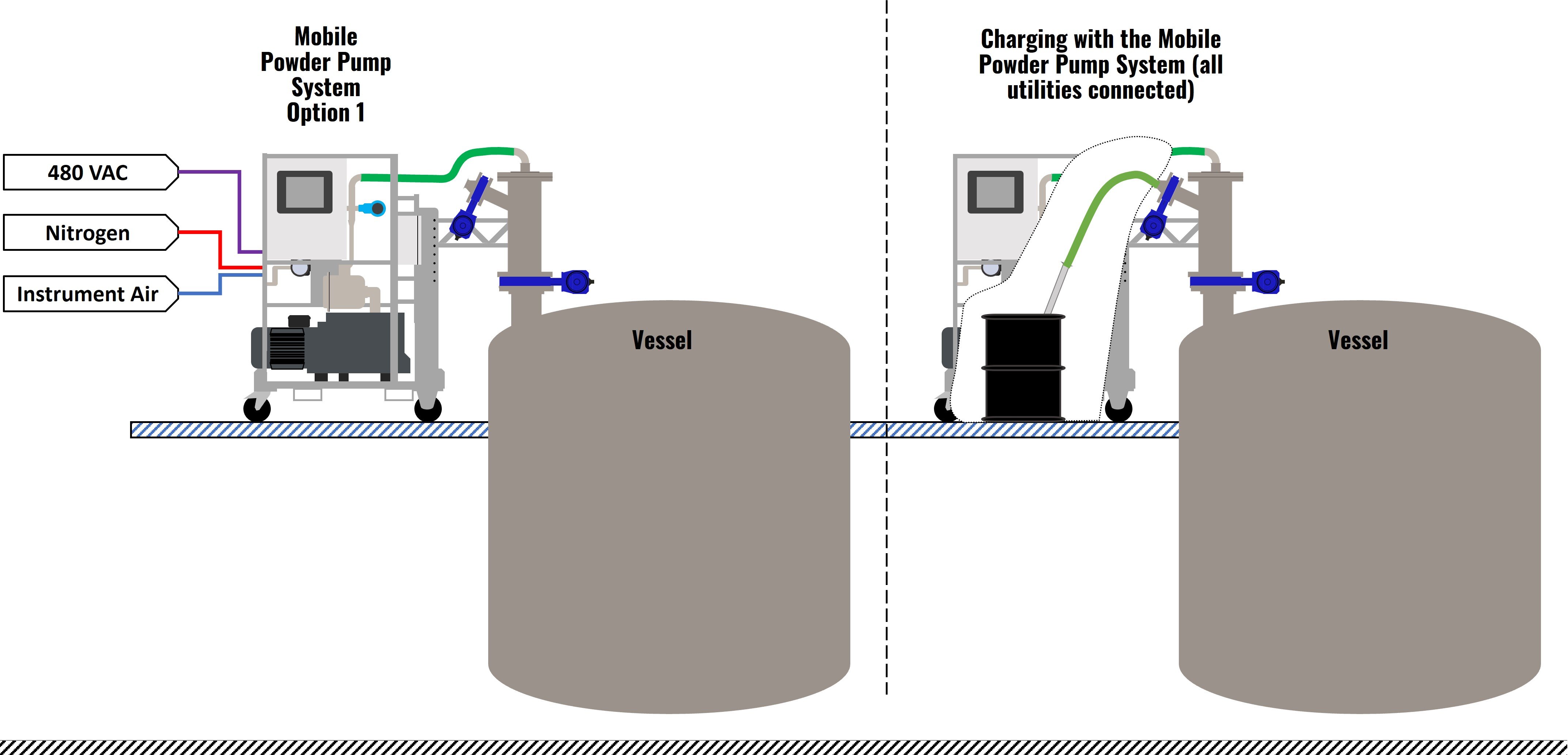
Overview:
A mobile conveying option provides flexibility by allowing the conveying system to be moved to different locations as needed. These systems can be cantilevered over a nozzle or installed directly on a vessel, making them highly adaptable to changing production needs.
Applications:
- Suitable for operations that require frequent changes in production layout.
- Common in industries where space is limited or where multiple vessels need to be served by a single system.
Benefits:
- Flexibility to move and adapt to different production setups.
- Cost-effective by reducing the need for multiple stationary systems.
3. Bulk Bag Unloading
Overview:
Bulk bag unloading systems are designed to discharge materials from large bags (often referred to as FIBCs or Super Sacks) into another piece of equipment, usually some type of conveying system. The bulk bag unloading station typically includes a bag lifting frame, support pan, untie chamber, and discharge flange to connect with downstream equipment. Additionally, things like bag massagers and spout closure devices are often implements to enable full discharge of product and a safe interface with the bottom spout of the super sack.
Applications:
- Ideal for facilities that receive materials in bulk bags.
- Used in industries like agriculture, food processing, and chemicals.
Benefits:
- Efficient and dust-free unloading of bulk materials.
- Reduces manual handling, improving safety and productivity.
4. Bag Dump Station
Overview:
A bag dump station allows operators to manually empty smaller bags of material into a pneumatic conveying system. These stations can be equipped with a dust collection port for connection to in-house dust collection or integral dust collection with internal filters and blower to reduce operator exposure to fugitive dust.
Applications:
- Best for operations dealing with smaller batches of materials.
- Commonly used in pharmaceutical, chemical, and food processing industries.
Benefits:
- Ensures a clean working environment by controlling dust emissions.
- Facilitates easy integration with pneumatic conveying systems.
For more information, check out our new Sureflow Bag Emptying Station.
5. Drum Unloading Station
Overview:
Drum unloading stations are designed to transfer materials from drums by tipping and/or inverting the drum. Other features can be included to aid in fully emptying the drum, isolate the drum from downstream equipment and ensure a high level of safety around the equipment during operation.
Applications:
- Suitable for industries that receive materials in drums.
- Used in applications where precision and cleanliness are critical.
Benefits:
- Safe and efficient unloading of materials from drums.
- Reduces manual labor and improves operator safety.
6. Multiple Vacuum Conveying Pumps with Single Vacuum Pump
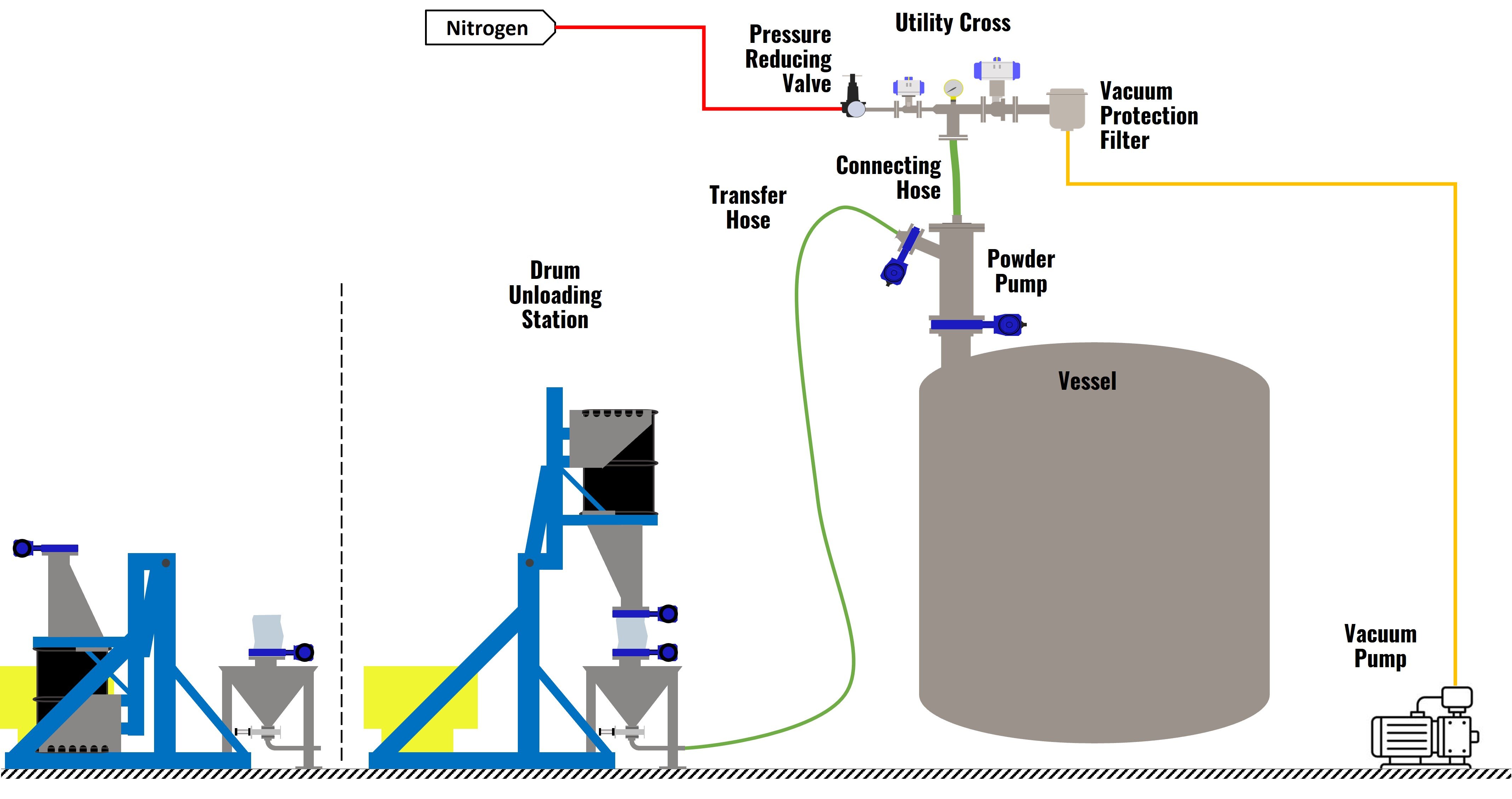
This system arrangement allows multiple Powder Pump systems to be operated using a single vacuum pump. Each conveying line can be independently controlled, allowing for flexibility within the system and a lower up front capital cost.
Applications:
- Ideal for complex operations with multiple conveying needs.
- Commonly used in industries that handle a variety of materials simultaneously.
Benefits:
- Centralized vacuum generation reduces equipment costs.
- Enhanced control over material transfer processes.
7. Feeding Multiple Vessels from a Single Source
Overview:
This arrangement allows a single material source to feed multiple vessels through a network of pneumatic conveying lines and diverter valve(s). Valves will be automatically positioned to enable charging to the desired location.
Applications:
- Suitable for large-scale production facilities.
- Used in industries like food processing, pharmaceuticals, and chemicals.
Benefits:
- Efficient distribution of materials to multiple points.
- Reduces the need for multiple material storage and handling systems.
8. Transferring from Multiple Feed Points to a Single Destination
Overview:
This configuration allows materials to be drawn from multiple feed points and conveyed to a single destination. It is useful in operations where materials from different sources need to be blended or processed together.
Applications:
- Ideal for blending operations or batch processing.
- Common in industries like food processing, chemical manufacturing, and pharmaceuticals.
Benefits:
- Streamlines the material handling process.
- Reduces the need for multiple conveying systems.
9. Direct Reactor Charge via Glove Box
Overview:
This system allows materials to be charged directly into a reactor vessel through a glove box, ensuring a high level of containment. It is especially useful in handling hazardous or sensitive materials.
Applications:
- Used in chemical and pharmaceutical industries where contamination must be strictly controlled.
- Suitable for processes involving highly reactive or toxic substances.
Benefits:
- Provides a safe and contained environment for material transfer.
- Minimizes the risk of exposure to hazardous materials.
10. Vacuum Conveying from Remote Mounted Glove Box
Overview:
In this arrangement, materials are vacuum conveyed via the Powder Pump system from a glove box that is remotely mounted from the reactor or processing equipment. This setup is beneficial in operations where space is limited or where the processing equipment needs to be isolated.
Applications:
- Ideal for cleanroom environments or facilities with strict contamination controls.
- Used in pharmaceutical manufacturing and high-purity chemical processing.
Benefits:
- Enhances safety by keeping hazardous materials contained and isolated.
- Flexible system design allows for remote operation.
11. Drum Filling/Pack-Off Stations
Overview:
Drum filling or pack-off stations are used to precisely fill drums with materials from various processes. De Dietrich has integrated these with both our Nutsche filter dryers and Powder Pump conveying systems. These stations are equipped with controls to ensure accurate filling and minimize spillage.
Applications:
- Suitable for operations that require precise packaging of materials into drums.
- Common in industries such as chemicals, pharmaceuticals, and food processing.
Benefits:
- Ensures consistent and accurate filling of drums.
- Reduces material waste and improves packaging efficiency.
Conclusion
Pneumatic conveying systems offer versatile and efficient solutions for the transportation of solids in various industries. Each of the system arrangements highlighted above is designed to meet specific operational needs, whether it’s handling hazardous materials, ensuring precise material distribution, or optimizing space and resources. By selecting the right configuration, you can enhance your material handling processes, improve safety, and increase overall productivity.
At De Dietrich, we focus on solving transfer needs by integrating equipment and controls to create automated, closed systems. Simply put, we design solutions – utilizing the Powder Pump System – to efficiently move your powder from one piece of equipment to another, while maintaining important aspects of the process including product integrity and operational safety. If you're considering implementing a pneumatic conveying system or upgrading your existing setup, it’s essential to assess your specific requirements and consult with experts to determine the best solution for your operation. The right system arrangement can make a significant difference in achieving efficient and reliable material handling in your facility. For more information on the different types of solutions we can provide, explore our Solutions Portfolio.